随着科技的不断进步和消费需求的不断变化,化工企业要在数字化、智能化、绿色化和高附加值化方面不断创新,其生产过程 中涉及到大量的原材料、设备和人力资源。传统的生产方式往往存在生产效率低下、资源浪费严重等问题。为了提高生产效率、降低成本、保障安全生产,化工企业纷纷寻求智能化改造的方法。
化工行业行业解决方案
化工行业数字化转型面临巨大挑战
化工行业作为传统的重工业之一,随着科技的不断进步和互联网的普及,信息化已经成为现代化发展的必然趋势。在信息化进程中也逐渐发展壮大。APS的实施,使得化工企业能够将数据和计算资源通过互联网进行共享和交换,实现资源的有效利用和成本的降低。

不稳定的需求预测
需求的不确定性会导致生产过剩或供不应求。通过整合先进的预测算法和实时数据分析,可以提高系统对市场变化的敏感性,从而更准确地调整生产计划。

物料计划不准确
库存高,供应与需求不同步,与生产计划衔接不够紧密,无法准确的通过系统计算物料需求规划与采购需求,造成停工待料,不能按需采购备料。

难以快速响应变化
设备故障等过程异常无法与计划排产真正衔接起来,计划无法及时应对异常情况及时调整计划,无法及时评估订单交期影响,没有到设别级的机台计划,主计划任务一旦下发后,企业就面临着生产过程“黑盒子”的问题,随着企业的不断扩大,生产进度只能依靠人工查询回复,费时费力,计划跟踪难度大

人工计划工作量大
各过程数据处理依托EXCEL及线下单据,人工处理数据工作量大、效率低、耗时长,计划跟踪完全依赖人工去检索,无法及时报工,及时调整计划。

柔性生产难应对
生产时多品种、小批量、频繁切换的产品

自动化程度低、人工环节多
整体自动化程度较低:内操操作强度高,自动化多是单步骤、散点式 人工操作不规范:人工操作环节多,行为难以管控,内外操协调和人机交互难度大,容易发生错投、漏投、多投、少投等。
供应链计划协同解决方案
场景应对方案
化工行业智能制造解决方案,以作业调度为核心,以降低生产成本、提高生产效率为目标,收集生产过程中的实时信息,并对实时事件及时处理,同时又与计划层和控制层保持双向通信能力,从而实现了整个生产过程的优化。
主计划
主计划可通过系统进行产能与计划模拟预排分析;预排主计划与各工序、机台计划安排情况。
产能平衡
通过主计划评估产能利用情况; 产能剩余时评估产能下备货订单满足产能需求。
物料齐套性分析
系统检查机台生产任务等物料齐套; 考虑库存、在职、采购在途对工单对物料供应; 根据齐套结果约束排产,拉动物料配送。
机台计划
获取主计划任务排出机台详细执行计划任务; 派工机台计划任务,机台按任务完成情况进行报工调整。
系统自动排产
系统自动完成工单排产、快速调整、插单; 自动获取生产现场进度滚动排产; 多约束多参数系统排产(产能、设备、人员)。
系统信息交互
设备、工艺、产能、工单等信息自动获取(ERP、SRM、APS、MES); 消除信息孤岛、透明共享。
项目亮点
通过易普优高级计划排程,帮助企业实现拉式精益生产,提高生产计划的准确性,快速应对变化,缩短制造提前期,降低库存,降低生产管理成本,提升企业竞争力。
排程优化,降本增效
通过固化计划员的排程经验并优化工序计划合理性,降低计划沟通成本和调度工作量,提升了计划体系的效率,计划制定时间缩短85%以上,同时也提高了物料准备和工装齐套性,实现了计划达成率20%以上的显著提升
精准备料,库存降效
APS系统准确的工序级计划,指导物流部门精准的备料,减少停机待料,降低在制品或线边库存15%以上
透明管控
APS系统实现车间的透明管控,让生产有条不紊的执行,让决策者对车间动态产能了如指掌
产能优化
APS通过模拟试算快速答复订单的交货期,最大化工厂产能,同时提升了客户满意度。
成功案例
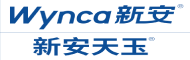